ALUSONG PVDF aluminum composite panel is exclusively made for exterior wall cladding, its excellent property comes from the front coating and its outstanding durability, PVDF kynar 500 coating is achieved through the continuing roller coating system which is based on the most prestigious technology and the multiple layers are individually stoved at 220-260℃, the two cover sheets sandwich the same mineral core of polyethylene which is Hardly inflammable. Chemical salt and alkali resistance for 20 years
PVDF coating, made of fluorine carbon resin, is solidified to dry film with super weather resistance. We have normal PVDF and NANO PVDF coatings. Normal PVDF coating, certified as KYNAR 500, is made of 2-3 time coating and baking, has good properties of anti-acid, Anti-alkali, is durable in atrocious weather and environment. Warranty could reach to 15 years for exterior use. NANO PVDF coating, with self-cleaning NANO meter paint on the normal PVDF coating, is used to protect the surface from pollution, dust or dirty rains. Warranty could be up to 15 years for exterior use.
Aluminum alloy | AA1100 AA3003 |
Aluminum skin | 0.21mm,0.30mm,0.35mm,0.40mm,0.45mm,0.5mm |
Panel thickness | 3mm,4mm,5mm,6mm |
Panel width | 1220mm,1250mm,1500mm |
Panel length | 2440mm,3050mm,4050mm |
Surface treatment | PVDF |
Colors | 70 colors, special colors available upon request |
Customers size | accepted |
GLOSSY | 20%-40% |
Panel width: ±2mm Panel length:±3mm
Panel thickness: ±0.2mm Panel diagonal: ≤5mm
Aluminum sheet thickness: ±0.01mm
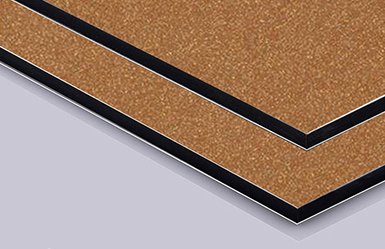
Raw material:
Base material: high strength aluminum alloy sheet
PE core material: non-toxic low density polyethylene
Surface coating: PVDF coating
Back coating: primer coating
Product properties
High resistance to peeling
Superior weather resistance
Light weight and easy to process
Excellent fire resistance properties
Coating evenness
Easy for maintenance
Impact resistance
1. Wall curtain, Cladding and Facade
2. Hotels and commercial mansions
3. Exterior renovation for old buildings
4. Subway and airports
5. Industry plants and materials,
6. Vehicle and boat materials
-
Application
-
Application
-
Application
-
Application
-
Application
-
Application
Description | Test standard | PVDF |
Thickness of coating | PVDF paint≧25um | 28um to 32um |
Coating flexibility (T-bend) | PVDF paint≥2T | 3T |
Color different | ΔE≦2.0(follow color sample) | ΔE<2.0 |
Pencil hardness | ≧HB | ≧HB |
Chemical resistance | 5%HCI or 5% NaOH test in 24 hours -No change;ASTM D1308 | No change |
Coating adhesion | ≧1grade for 10*10mm2 gridding test | 1grade |
Resist solvent | No change for 200 times(MEK) | No change |
Boiling water resistance | Coating no tear off for 2 hours | No TEAR OFF |
Peeling strength/stripping strength | Average ≧7N/mm of 180oc peel off for panel with 0.5mm alu.skin | 7N/mm |
Impact test for paint | 50KG.cm impact-paint no split for panel | No split |
Abrasion resistance (L/Mil) | ASTM D968 | 44 |
Temperature resistance | -40℃ to +80℃ temperature without change of color difference and paint peel off,peeling strength average dropprate ≦10% | Change of glossy only,no paint Peel off |
Coefficient of linear Thermal Expansion | 100℃ temperature difference | 2.4mm/m |
Detergent resistance (3%) | ASTM D2248 | No change |
Humidity Resistance (3000hrs,100%RH,100°F) | ASTM D2247 | No change |
Salt spray resistance (3000hrs,5% salt) | ASTM B117 | No change |
Resistance to Staining | 4000h radiate in 800W/m2 in humidity condition,glossiness deviation less grade 2,color difference ≦4.0 | No change |